July 16, 2022 - The Additive Manufacturing Alliance has begun holding roundtables with members of the White House. The goal of the discussions, which have been held twice so far, is to establish a dialogue between the Alliance and key federal policy makers.
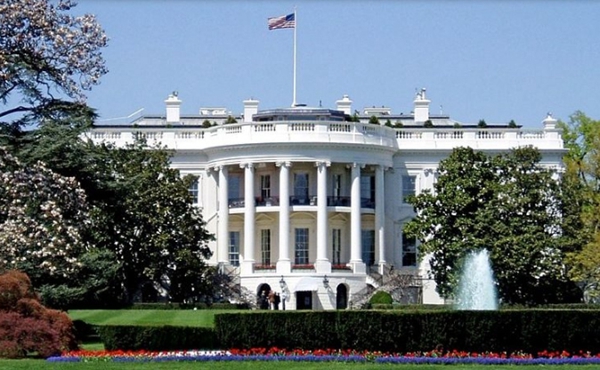
New roundtable between the White House and the Additive Manufacturing Alliance
The first roundtable was held on 22 April this year, where members of the trade association, heard from and shared ideas with Liz Reynolds, Special Assistant to the President for Manufacturing and Economic Development at the White House National Economic Council. There, Reynolds discussed the administration's policy approach to additive manufacturing, including the adoption of 3D printing for small and medium-sized enterprises (SMEs) in the federal supply chain. This strategy was later cemented in the Biden administration, with the AM Forward initiative announced in May this year.
Coalition members applauded Reynolds' stated goals, but also noted that there are already 3D printing companies that are trying to integrate themselves into the federal supply chain. However, they are having trouble dealing with the federal government. Fortunately, Reynolds held a second roundtable on July 12, where members of the Additive Manufacturing Coalition were able to discuss these issues in more detail.
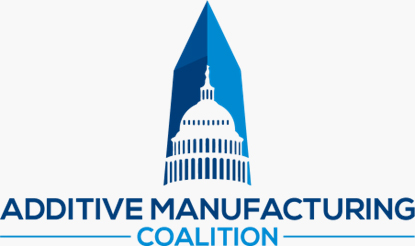
The White House heard suggestions from members of the 3D printing consortium, all of which are promoting cooperation between the technology and the government
New second roundtable
This time, members raised issues related to the current federal procurement process. This included basic issues, such as how to interact with appropriate entities such as the Department of Defense (DoD) and other agencies, as well as more complex issues. For example, intellectual property protection was raised, as well as issues faced in software development. Members also talked about restrictions on service and training contracts, which inhibit the ability of government agencies to adequately purchase printers and limit the effectiveness of maintenance, among other things.
All in all, the conversation raised awareness of the obstacles faced by the current government, and by stakeholders in the 3D printing industry. In particular, it makes clear that the federal government may need to revisit the issue of OEMs and subcontractors in relation to government procurement. Traditionally, the federal government, particularly the Department of Defence, has typically only worked with large prime contractors, such as defence companies, to manage the collaboration between subcontractors. This has made it difficult for SMEs to establish partnerships with federal agencies and enter the procurement process. For example, 3D printing companies that manufacture products for end users do not have the same access points as military subcontractors who make components for subassemblies of large government projects such as fighter jets. As a result, it may be difficult for 3D printing SMEs to work with the federal government, except through one of these prime contractors, as a single entity on a large project.
These roundtables are just the beginning of the Additive Manufacturing Alliance. In addition to holding more members-only events, and public webinars, they are also collating content from consultations with Reynolds and will forward a more detailed explanation of the issues raised to the Biden administration.
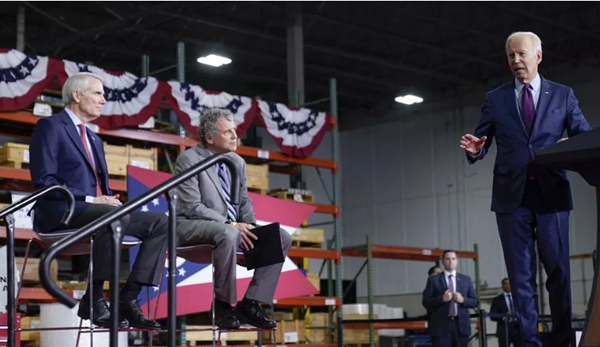
△White House pushes national plan to promote additive manufacturing
The White House's definition of 3D printing
The technology reduces the number of parts needed for an application and enables the production of small quantities of parts in a cost-effective manner. The technology allows for the manufacture of complex structures, such as internal channels for heat dissipation. The increased production capacity for customisation and the reduced need for specialised components combine to personalise products and reduce inventory requirements. Because the technology is built from scratch, rather than subtracting material that is then scrapped, these technologies can reduce material costs by up to 90% and cut energy use in half.
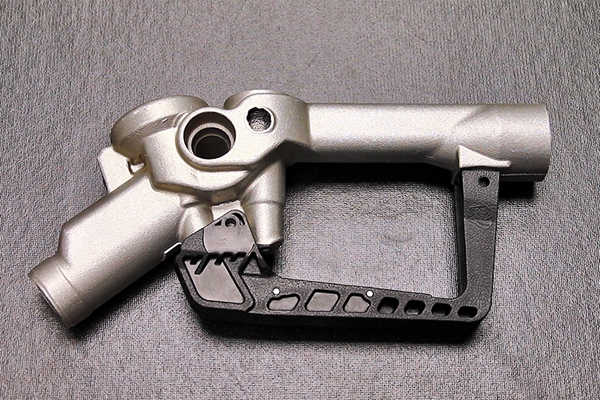
ΔThese vapour recovery fuel nozzles, which used to require manual assembly of six separate core components, now come as a single component. The final aluminium casting benefits from precise internal channels and small cross-sections that could not be produced by traditional metal casting methods
Examples of 3D printing include.
* Medical device companies using porous internal structures that could not be produced by traditional methods, through which the technique allows the creation of personalised hip implants sufficient to stimulate bone growth;
*The Air Force is 3D printing metal replacement parts as needed, rather than relying on expensive inventory or waiting years for parts made from hard-to-source components;
* General Electric's 3D-printed fuel nozzles for commercial aircraft engines, made from one part instead of 20 individual parts, offer a 30 percent cost savings; the new nozzles are 25 percent lighter and five times more durable;
*and, through the technology, increased resilience and competitiveness of the US supply chain, among others.