August 24, 2022 - To promote the economical, reliable and sustainable use of wood waste, US-based Forust3D has begun high-volume 3D printing of wood. To do this, it uses the speed, precision and quality of the adhesive jetting process to produce strong, lightweight wood parts. The company uses two types of wood waste as printing materials, namely sawdust and lignin.
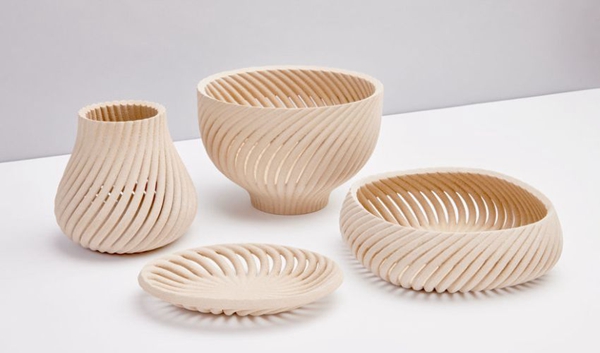
It is particularly important that Forust 3D aims to contribute to the materials recycling value chain and ultimately achieve net zero carbon emissions. According to the company, 15 billion trees are cut down each year worldwide to make paper, build houses and make furniture, which equates to 84 million tonnes of wood waste sawdust each year. Some of this waste is recycled and sold to downstream markets for the manufacture of particleboard or wood pellets for energy. Of course, there are many opportunities to recycle these waste products, which opens up the possibility of other routes.

Photo credit: Forust 3D
Additive manufacturing and Forust 3D
Forust 3D uses high-speed 3D printing technology to give new life to these discarded resources. The company uses wood waste to produce strong, beautiful and environmentally friendly wood products. The manufacturing process used was developed by DesktopMetal, which acquired Forust in 2021, and is based on the use of industrial sawdust waste as a 3D printing material for the mass production of furniture, construction, consumer goods and even luxury car interiors.
Forust 3D uses both small and large adhesive jet printers to manufacture products. This allows products to be manufactured at various scales: smaller printers for mass production and larger printers for mass production. The printing process begins with the application of sawdust to the build board, and then the machine's inkjet nozzles travel over the material, spraying adhesive and ink on the lignin to achieve the shape, which is one of the features of Forust 3D's printing process. In terms of the materials used, the company does not need to use additional adhesives as the lignin from the wood waste is used as a binder, creating another environmental benefit.
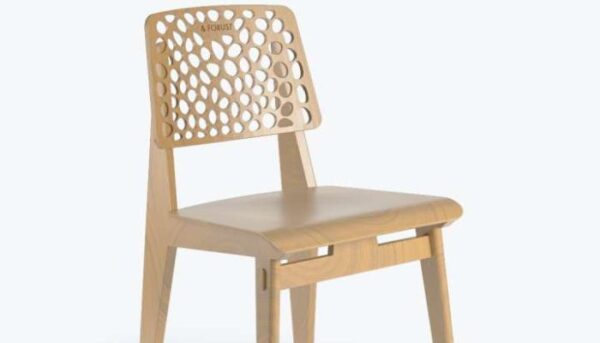
Photo credit: Forust 3D
Forust 3D's adhesive jetting process not only offers the ability to print grain-free, smooth wood surfaces, but also demonstrates an unprecedented technique for simulating realistic wood grain through wood products. This effect can make the final product virtually indistinguishable from natural wood. This can be particularly interesting for designers as it allows them to create complex organic shapes that are more difficult or almost impossible to achieve in normal wood manufacturing.