CNC processing plastic respective advantages and disadvantages introduced to help you choose the right processing material
Today and you introduce someCNC plastic respective characteristics to help you better choose the right material for you
01.ABS plastic
ABS is a comprehensive general-purpose plastic. It offers high impact strength, toughness and resistance at a low price. It is also easy to finish, as it can be easily painted, glued, or welded together. It will have a matte finish if left as is.
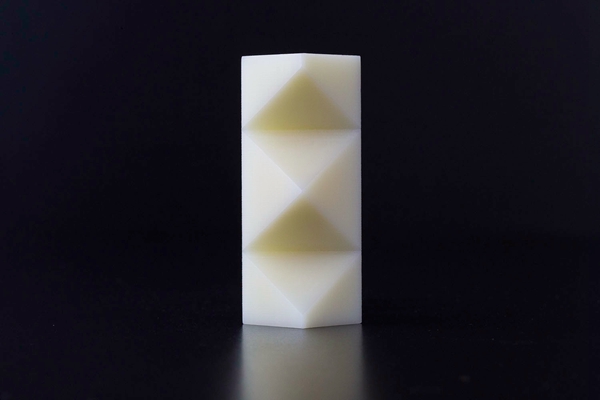
Pros: ABS is the best choice for general purpose prototypes, preformed prototypes, parts that will take a beating and need toughness, or when low cost is needed.
Cons: ABS does not have good abrasion or chemical resistance and will melt in acetone. It is also not a particularly strong plastic. Also.
Common Applications: The most common application for ABS is injection molding, used to make electronic housings, household appliances, and even the iconic Lego blocks.
02. Nylon
Nylon is a strong and durable plastic that is suitable for a variety of applications.
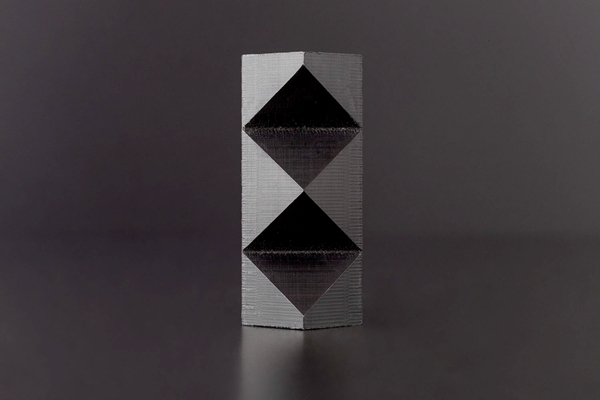
Benefits: Nylon has high strength and stiffness, holds up over a wide range of temperatures, has good electrical insulation, and good chemical and abrasion resistance. Nylon is ideal for applications requiring low-cost, rugged components.
Disadvantages: Nylon can absorb moisture, causing it to swell and lose some dimensional accuracy. Due to the inherent internal stresses in the material, it can also distort if there is a significant amount of asymmetric material removal during processing.
Common Applications: Nylon is most commonly used in medical devices, circuit board mounting hardware, automotive engine compartment components, and zippers. In many applications, it is used as an economical alternative to metal.
03.PMMA
PMMA is acrylic, also known as plexiglass. It is tough, has good impact strength and scratch resistance, and can be easily bonded using acrylic cement.
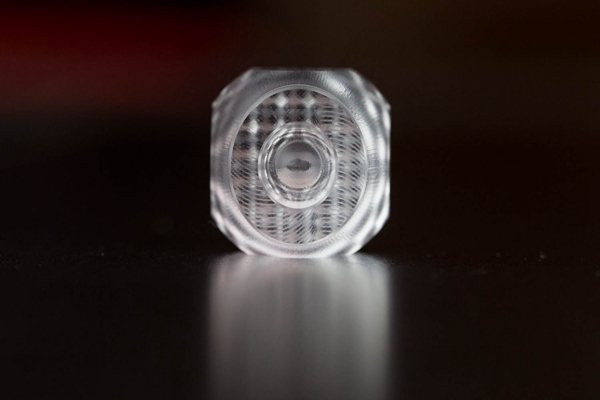
Pros: It is ideal for any application that requires optical transparency or translucency, or as a less durable but less expensive alternative to polycarbonate.
Cons: PMMA is a brittle plastic and it will fail by cracking or breaking rather than stretching. Any finish on a piece of acrylic will lose its transparency and take on a frosted, translucent appearance. Therefore, it is usually best to pay attention to whether PMMA parts should be kept in stock thickness to maintain transparency. If transparency is required on the machined surface, polishing can be done as an additional post-treatment step.
Common applications: After processing, PMMA is transparent and is most often used as a lightweight substitute for glass or light pipe .
04.POM
POM is a special brand of acetal homopolymer with a smooth, low friction surface, excellent dimensional stability and high stiffness.
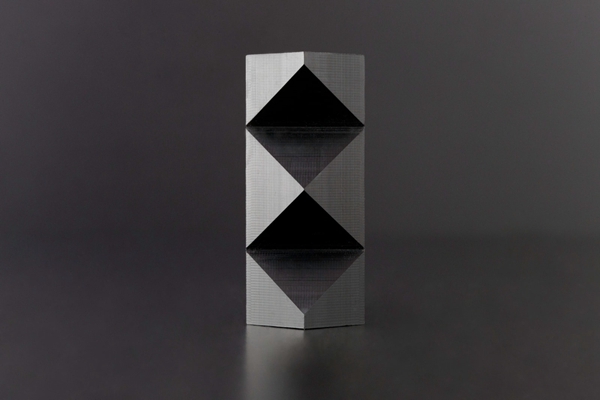
Advantages: POM is a good plastic for these or any other applications that require a lot of friction, require tight tolerances or need high stiffness materials.
Cons: POM is difficult to bond. The material also has internal stresses that make it susceptible to warpage in areas that are thin or have a lot of asymmetric material removal.
Common applications: POM is commonly used in gears, bearings, bushings and fasteners, or in the manufacture of jigs and fixtures for assembly.
05. HDPE
HDPE is high density polyethylene.
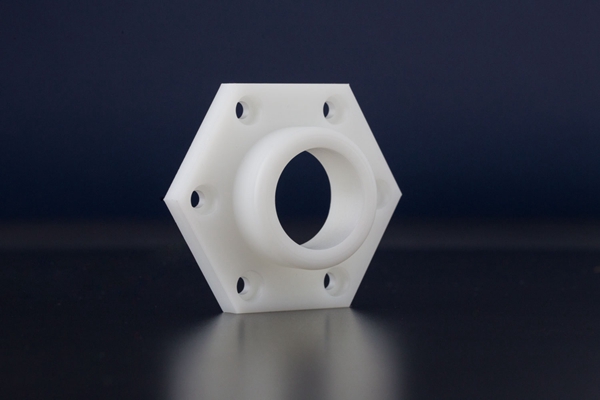
Advantages: HDPE is a very low density plastic, which also has excellent chemical resistance, electrical insulation and smooth surface. Because of its chemical resistance and sliding properties, it is ideal for making plugs and seals, but is also a good choice for weight-sensitive or electrically sensitive applications.
Disadvantages: The main disadvantage of HDPE is its poor strength, especially in stretching and bending.
Common Applications: HDPE is commonly used in fluid applications such as fuel tanks, plastic bottles, and fluid flow tubes.
06. PC
PC is our most durable plastic.
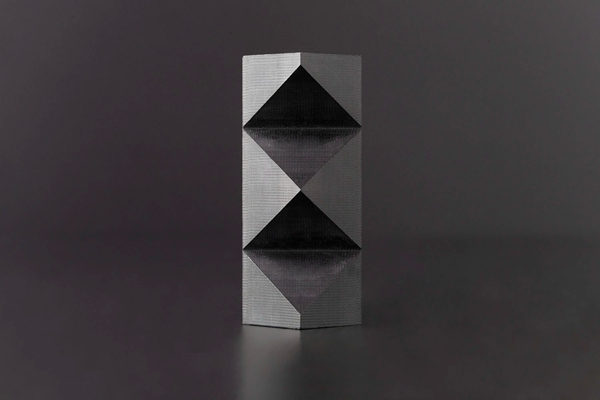
Benefits: It has high impact resistance and stiffness, and remains functional over a wide temperature range. It is also optically transparent and can be dyed black if opaqueness is desired. PC is best suited for applications that require a very hard or very strong plastic, or where optical transparency is required. As a result, PC is one of the most used and most recycled plastics.
Disadvantages: Pure PC does not have good abrasion resistance and scratches easily. If desired, a scratch-resistant coating and steam polishing can be added as a post-treatment step to improve abrasion resistance or optical clarity. It is also not readily available in two-inch thick parts, which limits the size of PC parts.
Common applications: PC's durability and clarity mean it can be used to make optical discs, safety glasses, optical tubes, and even bulletproof glass.