Mohou.com understands that American prosthetic manufacturer Psyonic has developed the first functional bionic arm on the market with multi-touch feedback, but at half the cost of similar products, in cooperation with 3D printing technology service providers.
Recently, Mohou.com understands that American prosthetic manufacturer Psyonic has developed the first functional bionic arm on the market with multi-touch feedback, but at half the cost of similar products, in cooperation with 3D printing technology service providers.
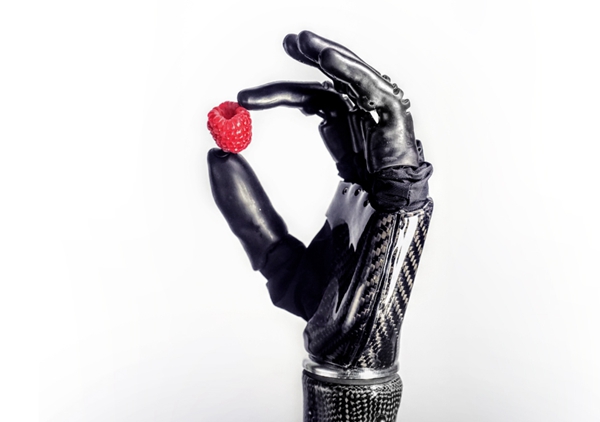
△Psyoni claims that Ability Hand is the first touch-sensitive bionic hand
The company opened the bionic arm Ability Hand, fingertips with sensors, when the user grip objects can detect pressure, and send vibrations to the arm to convey this feeling. It allows the user to feel what he or she is doing and handle even the most delicate objects. According to Aadel Akhtar, CEO of prosthetics manufacturer Psyonic, "With 3D printing technology, it's not only a game changer for our business model, but also for the entire industry." Both companies are now a step closer to using 3D printing technology to develop low-cost prosthetic limbs. Typically, traditional prosthetics are fragile, crude, expensive and outdated. According to Psyonic, "they are out of reach for the 90% of patients who can't afford advanced prosthetics."
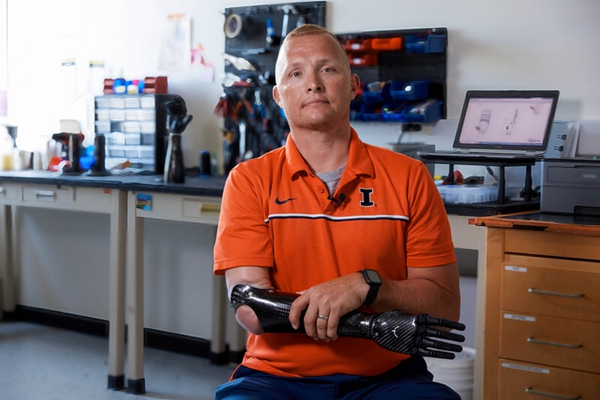
△ Sgt. Garrett Anderson and his custom 3D printed bionic arm
A Sergeant Garrett Anderson, who was discharged from the Army due to injuries, needed a custom prosthetic arm after his military service in 2005. He stated, "For the first time, I could feel my daughter's hand as well through my prosthetic arm."
Psyonic used Formlabs' Fuse 1 selective laser sintering (SLS) 3D printer. The process involves rapid prototyping, followed by iterations of changes, and the production of parts at a relatively low price and in small batches.
We have developed advanced bionic limbs that are affordable and available to everyone," Akhtar said. We would not have been able to create this type of bionic arm if we had not used Formlabs printers for manufacturing."
James Austin, lead mechanical engineer, said, "I think that hybrid manufacturing and adopting a production model that addresses customized needs is very important for startups in general, and for Psyonic in particular. if we had remained in a traditional manufacturing model, we would not have been able to compete with the larger prosthetic companies. Processes like CNC machining and injection molding, with their higher initial costs, especially trying multiple iterations of prototypes, are astronomical to us."
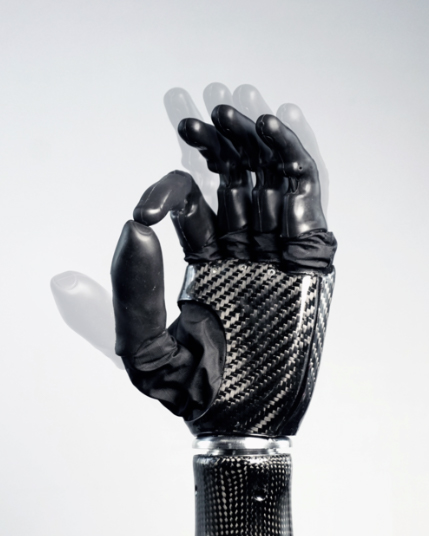
△ The company claims that with 3D printing technology, the new prosthetic is not only cheaper, but also more capable
3D printed Ability Hand bionic arm
The prosthetic arm weighs just 490 grams, which is less than the weight of a typical adult hand. The Ability Hand is charged using USB-C and can be fully charged in approximately one hour and can run all day on a single charge.
Most external electromyography (EMG) direct control systems, linear sensors and force resistors are compatible with the 3D printed bionic arm. According to Psyonic, each finger of the Ability Hand can withstand blunt force strikes without breaking, and it is both lightweight and waterproof.
Users can also take their bionic arm and connect it to Psyonic's mobile app (which supports iOS and Android) so that their prosthetic engineer can make remote adjustments to the device in order to allow users to continually enhance their grip and use.
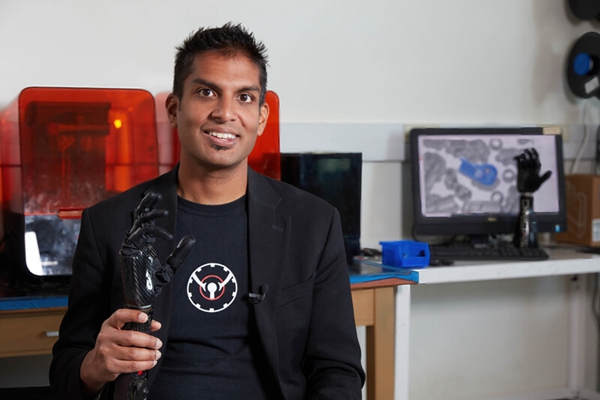
△Psyonic Founder and CEO Aadeel Akhtar
The Process Behind Psyonic's 3D Printed Prosthetics
In addition to 3D printing technology, the company developed the bionic arm using hybrid manufacturing techniques, such as silicone injection molding, and CNC machine tools. The company believes the Ability Hand has the potential to restore patients to their former quality of life and athletic ability.
During development engineering, the company collected extensive user feedback and then conducted in-house rapid prototyping to enhance the design and functionality.
According to Psyonic, the use of a hybrid manufacturing production method means that the prosthesis can be sold at an affordable price. In the past, Psyonic estimated that only about 10 percent of the population could afford custom prosthetics; now, by using this new method, that number is expected to increase to 75 percent. To produce long-lasting end uses, the company also uses stronger 3D printed materials that are impact resistant and robust.
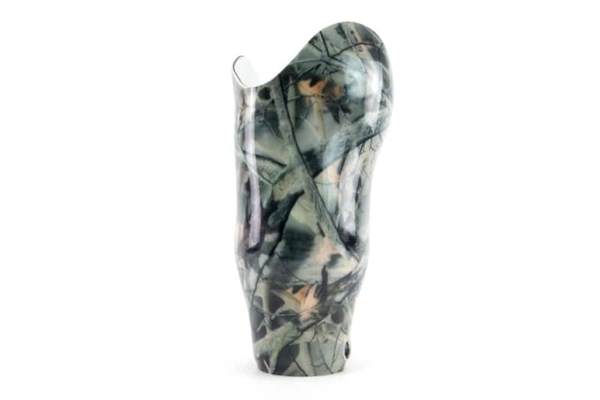
△ Protosthetics' 3D printed prosthetic inserts
Producing prosthetics through 3D printing
Amputees located in a remote area of Guatemala, in the maritime non-profit organization Island Missions Support, have started to make Raise3D E2 3D, to manufacture more durable 3D printed prostheses. The team had previously attempted to use the Prusa i3 MK3S+ and Raise3D E2 3D printers and PETG materials to create prosthetic limbs, but the country's hot weather conditions caused their materials to warp and fail to print. However, the team is now able to print child- and adult-sized hands and arms, restoring the ability of these amputees to accurately grip common objects.
Elsewhere, 3D printed prosthesis manufacturer Protosthetics has introduced what it claims is the first in the field, a full-service prosthetic 3D printing system for orthotic and prosthetic (O&P) fitting. The plug-and-play system, named "Galileo," is designed to overcome the clinical barriers to 3D printing technology for O&P implants.