Introduction, for the consumer goods industry, the race to market is now a race to the bottom, as brands need to accelerate the development of new packaging designs to meet changing customer needs in order to stand out in the face of intense competition. But changing packaging designs can be costly, especially in the bottled beverage industry. Typically, beverage companies use blow moulding to create traditional metal moulds, which means weeks of waiting time and thousands of dollars in mould opening costs. Is there a faster, cost-saving way?
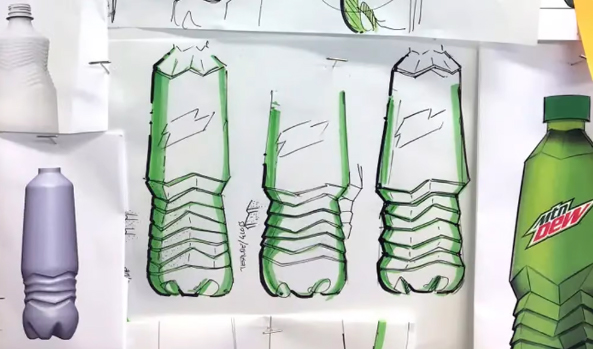
△ Pepsi's bottle design development process, from paper to digital to 3D printed mould prototypes
June 8, 2022 - Pepsi is increasing speed, reducing costs and expanding flexibility by using3D printing technology to create bottle moulds. In the past, Pepsi would spend up to $10,000 to produce a single metal mould (depending on the complexity of the packaging), says Max Rodriguez, senior manager of global packaging R&D, advanced engineering and design at PepsiCo Research. It takes about four weeks to machine the metal mould using traditional manufacturing methods, and then an additional two weeks to obtain the pilot unit, which is then blow-moulded.
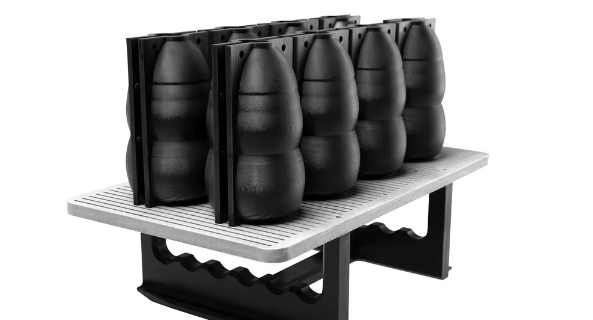
△ 3D printing to make a bottle mould using Henkel's xPEEK 147-Black material on Nexa3D NXE 400
3D printing to speed up prototyping to speed up production
In order to capture the market and bring drinks to market faster, 2 core issues needed to be addressed, reducing prototyping time and mould opening costs, hence Pepsi started using 3D printing technology a few years ago. Although 3D printers were excellent at producing design prototypes, early 3D printed moulds lacked durability. When 3D printed moulds were used in blow moulding machines, they could only produce about 100 bottles before the moulds started to fail. This prompted the company and his team to explore the use of hybrid methods, combining parts from traditional metal moulds with 3D printed structures.
In 2020, PepsiCo patented this hybrid model, first by creating a metal shell through a blow moulding machine. The company then went on to explore how to use 3D printing technology to create only the internal parts of the mould.
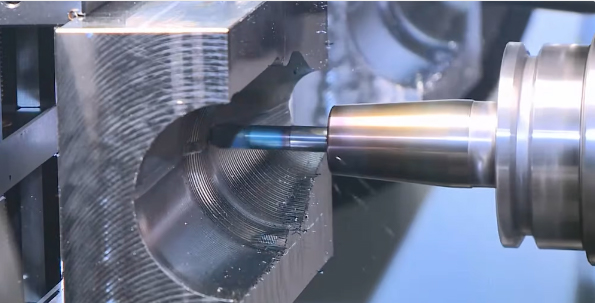
ΔBlow moulds are traditionally machined from metal, a slower and more expensive process than 3D printing
Exploring 3D printing solutions
Soon, the Pepsi team is working with Chicago-based 3D printing technology distributor Dynamism to explore industrial 3D printing solutions that can meet size and material requirements. Between 2020 and 2022, they conducted validation trials on a blow moulding machine to produce bottles at a rate of 600 to 800 bottles per hour using a single hybrid mould. By this time, initial progress had been made on the modular mould set concept, but the durability of the material was still not up to scratch. "In solving the mould generation solution using 3D printing, we focused on finding a material that would meet the production criteria," says Rodriguez. "In blow mould heat-setting applications, the moulds need to be heated to approximately 140oC degrees and need to withstand a blow pressure of 40 bars."
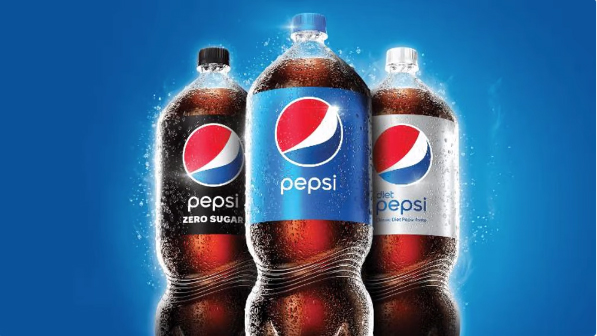
Δ2020 Pepsi bottle redesign
According to Rodriguez, Henkel introduced XPEEK147 about a year ago, which offers several advantages of cyanate to meet the design requirements. And then the team applied a dental stone backing to the printed insert to give the mould cavity the compressive strength required for blow moulding pressure. It then used a modified Blow Molding Technologies' Blowscan stretch blow moulding machine to produce the actual test bottles. rodriguez said that for the past few months, PepsiCo had been using a hybrid approach to produce the bottles. "First of all, the visible see shortened production times and cost savings, but more importantly, this hybrid approach, which allows flexibility to achieve different design iterations for multiple products so that we can evaluate all downstream market activities. This has really helped us with product rollout."
Ultimately, Pepsi chose Henkel Loctite's Nexa3D NXE 400 because it was large enough to print multiple moulded parts at the same time and was fast enough to speed up the iteration and production process.
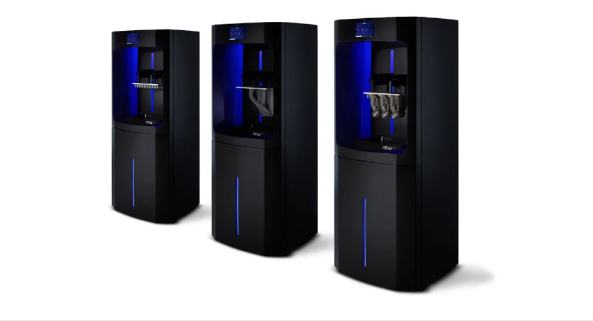
△Nexa3D's NXE 400 3D printer
4 weeks reduced to 48 hours, 10,000 cost becomes $350
Now, with 3D printing technology, a complete set of moulds can be completed in 12 hours, with 8 hours for 3D printing and 4 hours for post-processing or curing. The cost of each set of moulds is approximately US$350. These hybrid manufactured moulds can be used for over 10,000 bottles before they fail. The result is a cost reduction of almost 96% compared to traditional metal tools. says Rodriguez, "We expect the development cycle to be 30% faster." However, it's not just about the ability to 3D print mould sets. "It also has to do with the fact that the technology can be combined with our data analysis capabilities, so by jointly utilising these advanced tools, development cycle times can be increased even faster."
Going forward, will metal 3D printing be the next step for the company? "Metal 3D printing of blow moulds is in the works," says PepsiCo.