Mohou.com, June 10 - A group of researchers at the University of Oklahoma has developed a 3D printed model of a human ear for standardised blast exposure testing of hearing protection devices (HPDs). According to the researchers, the use of 3D printing technology could significantly improve the evaluation of HPDs by increasing personalisation, cost-effectiveness and time efficiency.
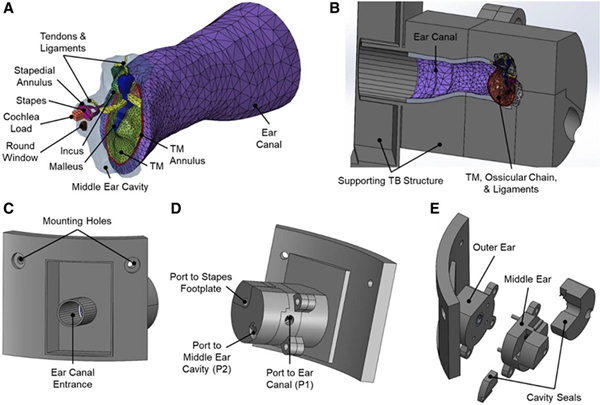
CAD model of a 3D printed ear model. Image from Otology and Neurology Open.
Benefits of 3D printed models
Generating realistic and accurate representations of the human form is essential for anatomical knowledge for teaching, surgical preparation and training opportunities, and this is where the benefits of 3D printing technology can play a key role. For several years now, 3D printing has been used to produce accurate, patient-specific 3D printed anatomical models with greater colour fidelity, saving hours of surgical planning time. As 3D printing technology matures, more and more 3D printing companies are obtaining ISO certification and FDA clearance for their 3D printed models.
On-the-fly 3D printed anatomical modelling services are also becoming increasingly popular, with companies such as Stratasys and Ricoh USA partnering to provide 3D printed models to healthcare facilities, and Fast Radius and Axial3D offering a new 'DICOM to Print' service for use in hospitals across the US.
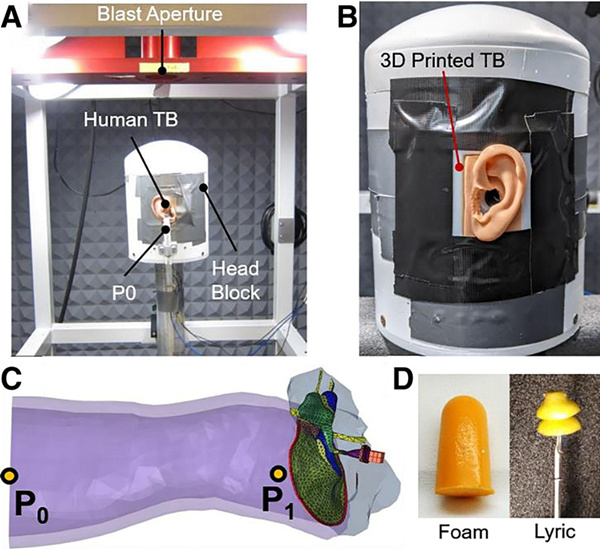
Experimental shockwave setup and pressure transducer placement for measuring shockwave transmission in a 3D printed ear model. Image from Otology and Neurology Open.
Improving HPD
In active combat situations, blast-related ear damage (e.g. tympanic membrane (TM) rupture) can lead to hearing loss. HPDs are required to prevent hearing loss when deployed in hazardous situations, and although a variety of HPDs are widely available, some forces believe that HPDs reduce situational awareness. Advanced HPDs are designed to improve perceived situational awareness and HPD compliance, but current research suggests that further improvements to HPDs are still needed, as well as more reliable and effective testing procedures.
The ability of various HPD earplugs to protect against noise pulses or blasts has been studied using human cadaveric temporal bone (TB) and various computational and experimental methods. For their study, the Oklahoma team developed a 3D printed model of the TB made of a flexible and rigid polymer containing the TM, ear canal, middle ear suspensory ligament and tendon, auditory chain and middle ear cavity.
The model is a mechanical and anatomical replica of the middle and outer ear that allows HPD to be measured and assessed during blast exposure. experiments were conducted to expose the 3D printed ear model to blasts with and without HPD. The pressure at the entrance to the ear canal and near the TM in the ear canal was recorded and the results were then compared to cadaver TB for validation. The team also assessed the potential of the model to be used as an acoustic transmission model.
With the HPD installed, the decay peak pressure near the TM was as low as 0.92 psi and the blast peak pressure at the entrance to the ear canal was 5.62 psi, while without the HPD, the pressure near the TM was 9.79 psi, a similar peak at the entrance to the blast ear canal. The study therefore accurately assessed the protective function of the passive HPD during the blast and demonstrated the efficacy of the 3D printed model for HPD standardisation testing.
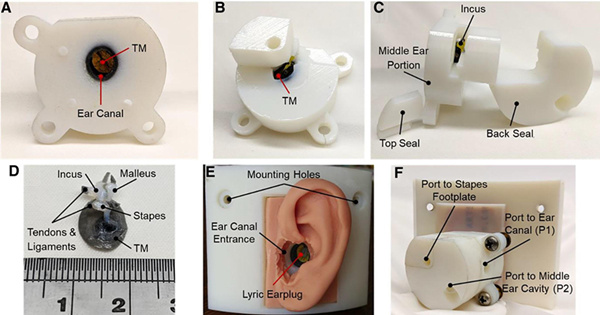
3D printed image of the completed print of the unassembled middle ear portion of the TB. Image from Otology and Neurology Open.
3D printed custom hearing devices
Hearing aids are one of the most important examples of how personalised medical devices can benefit from the development of 3D printing. In fact, researchers at the US Army Aeromedical Research Laboratory have previously used the technology to produce and test customisable earplugs for members of the US Armed Forces. This new technology for producing ear protection could be deployed in the future to prevent hearing loss in members of the armed forces.
Elsewhere, companies such as Materialise, EnvisionTEC, Formlabs and Sonova have been 3D printing hearing aids and custom headphones for years, and it is estimated that 99% of hearing aids worldwide are now custom manufactured using additive manufacturing.