3D printing offers new ideas for the development of patient-specific orthoses that can address the limitations of currently available technologies. However, to date, there has been little research into customised foot orthoses and there is a lack of relevant manufacturing process steps.
Introduction: In clinical applications, specific foot orthoses are often required to solve patients' foot problems. Until now, traditional manufacturing methods for customised functional foot orthoses (FO) have mainly been plaster casting and hand fabrication, with orthotic treatment depending entirely on the skills and expertise of the individual practitioner, making manufacturing procedures difficult to standardise and replicate, as well as being expensive, time-consuming and wasteful of materials.3D printing offers new ideas for developing patient-specific orthoses that can address the limitations of currently available technologies . However, to date, there has been little research on customised foot orthoses and a lack of relevant manufacturing process steps.
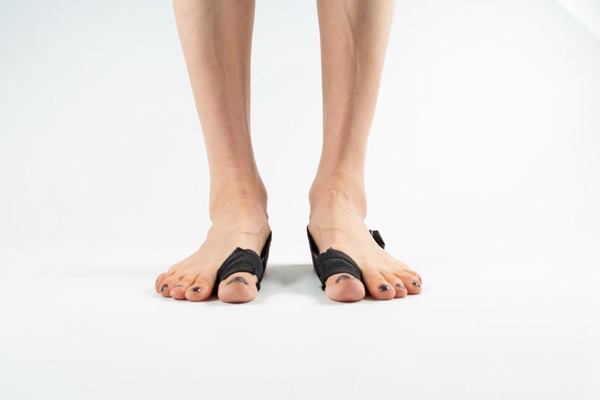
In June 2022, researchers from Italy published a study in Materials entitled Foot Orthosis and Sensorized House Slipper by 3D Printing.
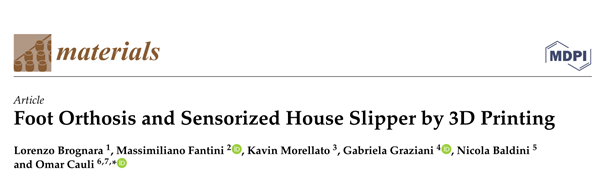
The study
In this study, the authors present a feasibility study that involves interdisciplinary collaboration between industrial engineers and podiatrists.
(i) 3D scanning technology was used to obtain data on the patient's foot and compared with conventional casting.
(ii) A GD workflow was created to design a process that would allow easy customisation of the orthotic shape, enabling the end user (podiatrist) to customise the orthotic interactively with the patient.
(iii) Comparisons were made between different printing materials to assess the mechanical behaviour of the orthoses. The researchers used a standard material (polycarbonate sheet) (hand-formed), which was compared with four sets of 3D printed samples: polyethylene glycol (PETG), polyacrylonitrile-butadiene-styrene (ABS), polycarbonate (PC) and polylactic acid (PLA) (manufactured by fused filament fabrication (FFF)).
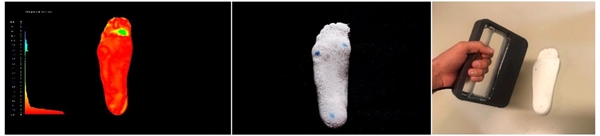
△ Comparison of ten plaster models obtained after recording footprints in neutral position with pinprick method and sub-ankle bandage
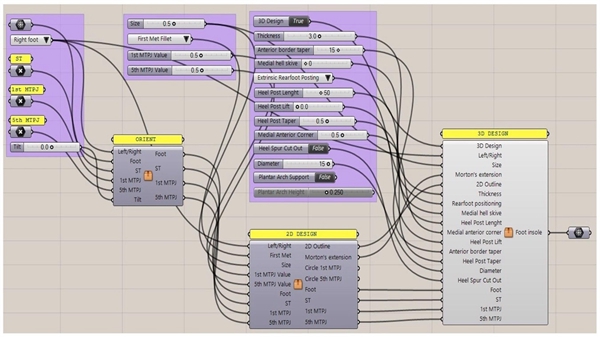
△Design workflow for interactive modification of foot orthoses
Phenomena
Medical staff and inexperienced users can design a customised foot orthosis in less than 5 minutes. The discrepancy between the produced foot cast model and the real foot model created using 3D scanning is the result of the non-smoothness of the patient during the information collection process.
Podiatrists with computer aided design (CAD) capabilities can easily create custom foot orthoses to meet the clinical needs of their patients using the established GD method. The complex shape of the orthosis can also be easily and quickly recreated by 3D printing.
Compared to standard polycarbonate sheets, all printed materials have a certain yield stress and are less prone to deformation. The print orientation and the forces applied during the printing process may have an impact on the printed product, and the research will require more testing in different print orientations and mechanical loading conditions to determine which materials are more suitable for everyday life and medical needs.
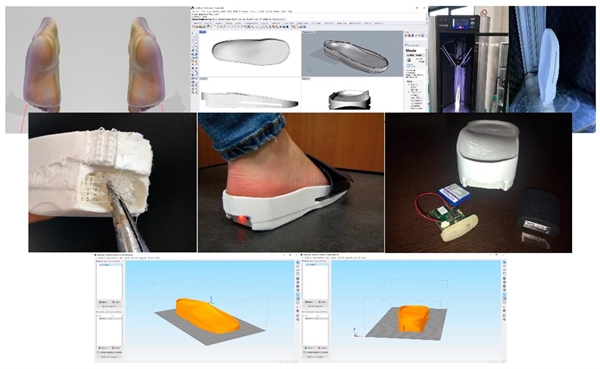
Key steps in the modelling process of the △inductive slipper
Conclusion
This research provides a new technique for the production of customised foot orthoses. The process is economical and simple for professionals and is highly feasible. The study demonstrates that the process of capturing patient information with a handheld 3D scanner will be more accurate. In terms of printing, the study proves that polymer materials can have a significant impact on the manufacturing process in terms of mechanical quality.
Link to original article: https://www.mdpi.com/1996-1944/15/12/4064/htm