Among the many types of rehabilitation aids, the manufacture of orthopaedic devices is one of the areas that is currently most closely integrated with the application of additive manufacturing - 3D printing technology - and is still being optimised.
According to the data of the National Bureau of Statistics, the number of elderly people over 60 years old in China reaches 264 million in 2020; according to the Statistical Bulletin on the Development of Disabled Persons in 2020, the number of disabled people in China reaches more than 85 million, and a total of 2.246 million disabled people will be provided with various types of assistive devices in 2020, and the penetration rate of rehabilitation devices among disabled people in China still has more room for improvement. Based on the huge group of disabled and elderly people in China and the current low penetration rate of the rehabilitation aids market, China's rehabilitation aids market shows the characteristics of a large number of people in demand and a large market potential.
Among the many types of rehabilitation aids, the manufacturing of orthopaedic devices is one of the areas that are currently most closely integrated with additive manufacturing - 3D printing technology - and are still being optimised and developed. In the process of application development, 3D printing technology has been integrated with 3D scanning, digital design software and orthopaedic manufacturing needs, gradually forming a complete digital design and manufacturing process, which has injected fresh "blood" into the innovation of orthopaedic devices and other rehabilitation aids. Inevitably, however, there are still many challenges in the field of 3D printed orthopaedic rehabilitation aids manufacturing. In this issue, we will take the forthcoming "3D Printing and Rehabilitation Aids White Paper, 3rd Edition" and use the manufacturing of foot and ankle orthoses as an example to understand the applications, challenges and trends of 3D printing in the manufacturing of rehabilitation aids with our friends in the Valley.
3D printing digital manufacturing of foot and ankle orthoses
Orthotics are assistive devices that help people with disabilities. The role of orthoses is to support and modify the structural and functional characteristics of the human neuromuscular and musculoskeletal systems. For patients with functionally limited impairments, orthoses are used to apply forces on the body and thus meet biomechanical needs. Orthoses can be divided into custom-made products and prefabricated products. Prefabricated products are relatively inexpensive and can be obtained quickly as off-the-shelf products. Bespoke orthoses are better suited to the patient's body and perform better. Traditional custom orthotics are labour-intensive manufacturing processes using plaster moulding techniques. Additive manufacturing - 3D printing - is the ideal technology to achieve customised production of such rehabilitation aids at scale and, thanks to digital technology, offers the possibility of reducing the reliance on manual experience, achieving repeatable quality and developing innovative orthopaedic products.
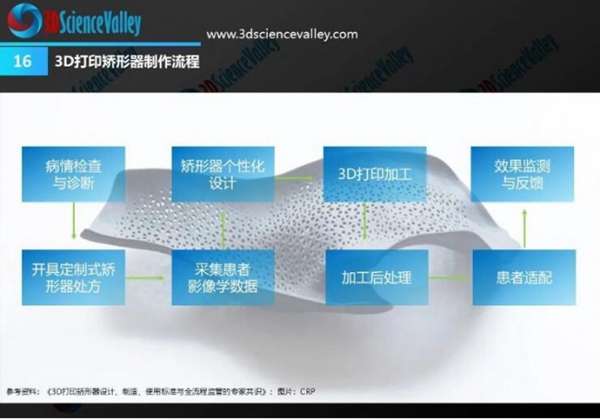
©3D Science Valley White Paper
The cost-effectiveness of additive manufacturing-3D printing for orthopaedic customisation and its potential for transformative services have been proven.
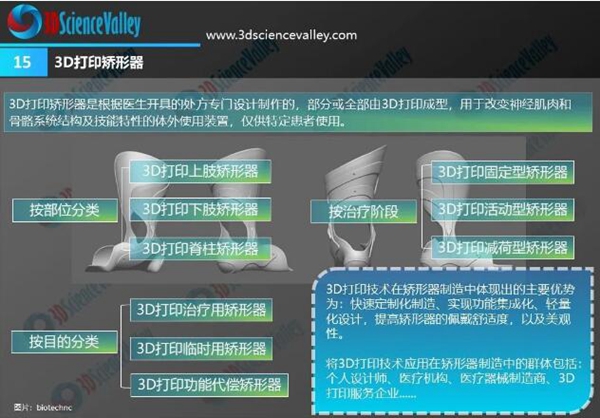
©3D Science Valley White Paper
Custom orthotic design and manufacturing involves three main steps: geometry capture, design and manufacturing.
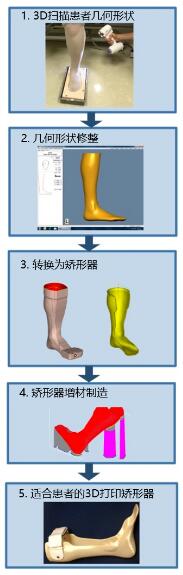
Foot and ankle orthosis 3D printing digital manufacturing process
The example in the diagram above illustrates the manufacturing process for 3D printing of a foot and ankle orthosis. Step 1 is a 3D scan of the patient's ankle and foot (the patient's plantar surface also needs to be scanned, either by scanning a foam print box or by scanning the patient's plantar surface directly). In step 2, the scan data is processed using CAD software to stitch the two scans together by aligning the reference points placed on the edges of the foam print box. the trim lines of the AFO are created and smoothed manually using CAD software. Step 3 is the conversion of the trimmed model into an orthosis; step 4 is the design of the 3D printing path and support structure for the foot and ankle orthosis; and finally, the printing of a customised orthosis to fit the patient.
In recent years, the medical community and research institutions have conducted research into the biomechanical design and performance of 3D printed orthoses. For example.
Some institutions have applied finite element modelling (FEM) and topology optimisation to design foot and ankle orthoses manufactured by selective laser sintering (SLS) 3D printing; some have investigated the use of nylon 12, glass-filled nylon 12 and nylon 11 materials and SLS 3D printing to manufacture passive foot and ankle orthoses, which offer sufficient stiffness and better damping than conventional carbon fibre orthoses.
Some studies integrate CAD model parameterisation and finite element analysis to quantitatively adjust, predict and experimentally validate the bending stiffness of foot and ankle orthoses manufactured by fused extrusion FDM 3D printing technology. Other studies have analysed the strain of conventional foot and ankle orthoses made from PP-PE versus FDM 3D printed foot and ankle orthoses made from PC-ABS and ULTEM™, showing that FDM 3D printing can produce stiffer AFOs with the potential for advanced lightweight designs.
Challenges and trends in block 3D printing
In limited clinical evaluations, additive manufacturing-3D printing technology has demonstrated the ability to create custom orthoses. In the upcoming "3D Printing and Rehabilitation Aids White Paper, 3rd Edition", you will be able to see cutting-edge international and domestic applications in the field of 3D printed foot and ankle orthoses and spinal orthoses, such as the collaboration between Centrin 3D and Ruiha International and Meizhao Scoliosis Studio through the 3D digital orthosis treatment solution process, which provides Chinese scoliosis patients with good body-following, aesthetic and breathable, comfortable and scoliosis orthopaedic brace with excellent orthopaedic results.
Numerous studies have also clearly demonstrated that additive manufacturing-3D printing has not yet been adopted in major clinical facilities for the mass production of customised rehabilitation aids such as orthoses. There are still several challenges that need to be addressed in order to drive the further development of 3D printing-additive manufacturing in this field, including: intelligent clinical and rehabilitation technician-friendly design software for 3D printed orthoses and other rehabilitation aids; improving the economics of printing materials and the productivity of 3D printing systems; and improving material strength.
The clinical and design interface is key to the adoption of additive manufacturing in the rehabilitation medical community. As seen in the previous article on the manufacturing process of 3D printed foot and ankle orthoses, in the process of digital design and additive manufacturing of rehabilitation aids, the application side needs to be able to acquire 3D scan data, modify the geometry of 3D surfaces, convert surfaces to solid objects and create trim lines through software. Software platforms tailored for 3D printing of rehabilitation aids such as orthoses are an effective way to achieve these goals. In the upcoming white paper you will be able to see what software development companies have achieved in 3D printing digital design of rehabilitation assistive devices, such as the unique 3D organic design system of Oqton's Geomagic Freeform software, which turns traditional 3D design implementation on its head and adapts the entire rehabilitation assistive device process including scanning and processing, custom design and 3D printing production. digital manufacturing process. You will also see artificial intelligence technology leading to smarter scanning model processing and orthotic design solutions for personalised orthotics.
Cost and manufacturing time are two other major barriers to the adoption of additive manufacturing - 3D printing - for rehabilitation aids such as orthoses. The initial investment in additive manufacturing equipment, especially industrial-grade equipment, is high. Of course, with the development of additive manufacturing-3D printing and the industry as a whole, the price of additive manufacturing equipment has dropped significantly and the material deposition rates and yields of the equipment have improved.
In addition, the mastery of advanced design techniques by designers of rehabilitation aids will also affect the cost and efficiency of 3D printing. Advanced designs such as topology optimisation and sparse structures, for example, offer the assurance of using 3D printing materials in an efficient manner and minimising manufacturing time. According to 3D Science Valley's market observation, the increased intelligence and automation of international software platforms tailored for 3D printing of rehabilitation aids such as orthoses will reduce the design challenges faced by designers of rehabilitation aids under this general trend, which is a positive contributor to 3D printed rehabilitation aids moving towards scalable adoption.
Safety and durability are also important for 3D printed rehabilitation aids. For example, the use of 3D printed orthoses under repetitive loads places demands on the ultimate strength and fatigue strength of 3D printed materials. The development of carbon fibre reinforced thermoplastic materials provides stronger materials for 3D printing applications of rehabilitation aids such as orthoses and prosthetic receiving cavities. Of course, quality control during the additive manufacturing process is also a factor that affects the safety and durability of 3D printed rehabilitation aids.
The application potential of 3D printed rehabilitation aids is mainly reflected in the optimization and innovation for the design of rehabilitation aids and the change of the treatment service model.
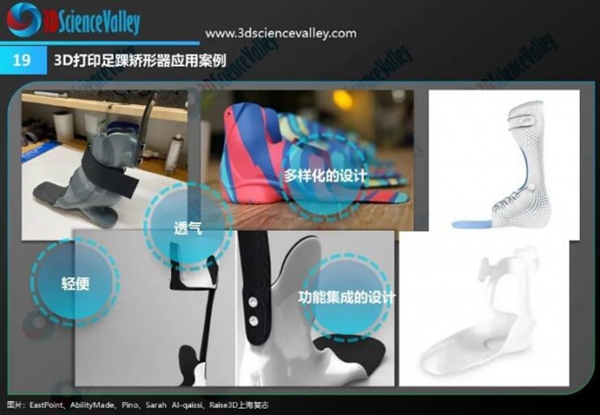
©3D Science Valley White Paper
In the case of orthoses, for example, the design of rehabilitation aids is not constrained by the same shapes and features as traditional products when using additive manufacturing - 3D printing technology - which allows for the design and manufacture of orthoses with greater functionality, complexity and aesthetics for better efficacy and fit, and faster delivery times, without increasing manufacturing time. In terms of treatment delivery models, 3D printing and digital design processes create the conditions for distributed design and manufacturing of rehabilitation aids. For example, clinicians may only need to 3D scan a patient and specify design requirements for rehabilitation aids such as orthoses, and geometric processing, design and optimisation can be done remotely from a cloud-based design centre. After approval by the clinician, the design can be sent over the internet to a 3D printing facility in the hospital or to any of the approved additive manufacturing facilities for manufacture, ultimately benefiting a wide range of patients.
Reference:
1.Ankle foot orthosis with exchangeable elastic elements
2.Manufacture of passive dynamic ankle-foot orthoses using selective laser sintering
3.Additive manufacturing of custom orthoses and prostheses
4.Patient specific ankle-foot orthoses using rapid prototyping
5.Dimensional accuracy of ankle-foot orthoses constructed by rapid customization and manufacturing framework
6.Additive manufacturing of personalized ankle-foot orthosis
7.A preliminary investigation into the development of 3D printing of prosthetic sockets
8.The development of a rapid prototyping prosthetic socket coated with a resin layer for transtibial amputees
9.Cost Modelling of Rapid Manufacturing Based Mass Customisation System for Fabrication of Custom Foor Orthoses