On July 2, 2022, SpaceX's 25th Commercial Resupply Service (CRS-25) mission will provide new scientific research support, supplies and equipment to the International Space Station (ISS) crew, including a 3D-printed plating mount. This support component was manufactured by NASA to house a new laser to determine the age of the rocks on its star. Once on the ISS, researchers will also test the 3D-printed part, including exposing it to outer space and other operations.
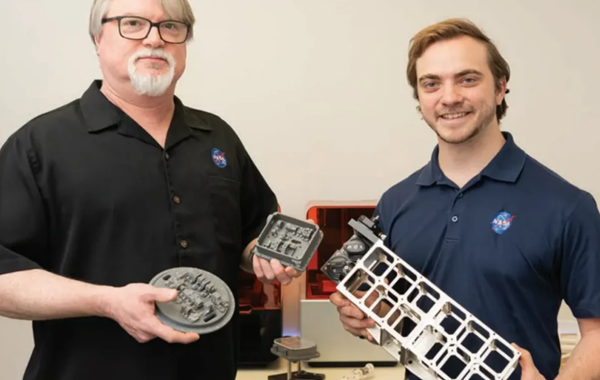
Small size, high performance laser
In a recent article published by NASA's Goddard Space Flight Center in Maryland, the agency talks about the goals of the experiment and the work being done on the ISS, as well as the role and impact 3D printing will have on the project's progress. According to the agency's publication in the Spring 2022 issue of CuttingEdge, the laser developed by Goddard physicist Barry Coyle fills a gap in existing technology, providing a powerful yet small and lightweight tool for future planetary missions that can explore how other planets form. In addition, the palm-sized laser is critical for small rovers and landers, reducing mission budgets.
Coyle's interest in lasers dates back to the 1980s, when he worked in the laser lab of Fred Watts, a professor of mid-physics at Charleston University in South Carolina, and found lasers difficult. He pondered why assembling lasers in one place was so important to production and cost efficiency in a NASA post in October 2021, while researching other space lasers at Goddard. The idea to build the laser in situ came to Coyle shortly after the launch of the Earth Science Laser Altimeter System (GLAS), the first laser rangefinder instrument for continuous global observation of the Earth.
Coyle noted, "Producing spaceflight laser systems outside of NASA is expensive and inefficient, and nothing saves time, energy and cost like 3D printing, which can greatly simplify the manufacturing process and assembly, making it an ideal solution for new "tiny" lasers and other The use of 3D printing technology can greatly simplify the manufacturing process and assembly, making it an ideal solution for custom parts such as new "tiny" lasers."
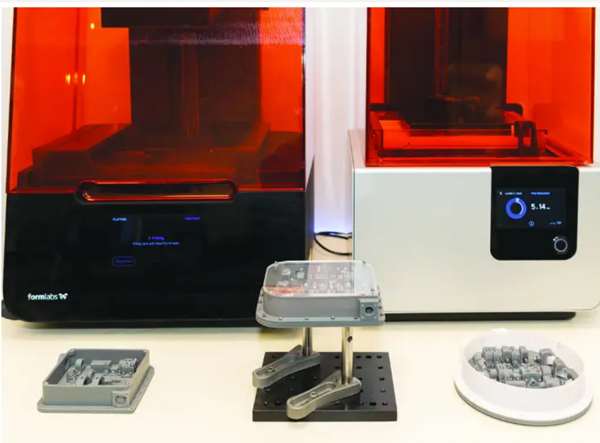
The △ palm-sized laser is attached to the mounting area by a plated bracket (silver) printed on Form 3. Image courtesy of NASA Goddard Space Flight Center.
Mounting bracket for the 3D printed laser
Unlike the large lasers on the Curiosity and Perseverance Mars rovers, this new laser is ideal for small sample observations. The laser is able to measure the composition of rock samples by separating molecules in the rock into atoms. However, the laser needs to have a correct and reasonable connection and mounting position to work properly. This is where 3D printing comes in handy. Engineers used 3D technology to quickly develop and improve the laser's mounting connection part.
To create the mounting bracket, NASA used Formlabs' Form 3 stereolithography (SLA) platform and the brand's Rigid 10K Resin, a glass-filled material that is the hardest material in Formlabs' engineering portfolio and can be used to make precision industrial parts that can withstand large loads without bending, which gives a smooth matte effect, and is highly heat and chemical resistant. Next, Goddard's NASA engineers relied on nTopology to generate design software to provide an organic support design for the bracket that maximizes load-bearing capacity. They then worked with Formlabs printers to optimize the bracket design for maximum strength.
According to Goddard engineer Matthew Mullin, "It's really exciting to be able to work with someone in a specialized field to design and manufacture 3D printed laser parts. Compared to traditional machining, 3D printing allows for different designs to be done faster and at a significantly lower cost. 3D printed laser components like this used to be custom milled from lightweight metals; now, advanced manufacturing techniques can reduce manufacturing time and costs."
Once the final printed parts were fabricated, the team sent their resin prints to RePliForm, a Maryland-based specialty company, for outer layer plating. Plating the Rigid 10K Resin printed parts increases the strength of the part and reduces the amount of exhaust emissions from the part, making the part much lighter than a traditionally machined part for the same application. In addition, thanks to 3D printing, Goddard's team can design, print, iterate and redesign in less time than a scramble machining process.
The laser will be launched from NASA's Kennedy Space Center in Florida on the CRS-25 mission by July 14, 2022, carrying SpaceX's robotic Dragon capsule and a Falcon 9 rocket. cRS-25 will fulfill part of an ongoing cargo contract between SpaceX and NASA and is the third mission for this special spacecraft .