11 July 2022 - British engineering company Renishaw has expanded its partnership with Welsh custom bike manufacturer AthertonBikes to help the latter develop its in-house 3D printing capabilities.
11 July 2022 - British engineering company Renishaw has expanded its partnership with Welsh custom bike manufacturer AthertonBikes to help the latter develop its in-house 3D printing capabilities. The bike manufacturer is looking to develop more durable, World Cup-winning bikes by transferring the additive manufacturing process in-house and reducing part manufacturing times. Dan Brown, co-founder of Atherton Cycles, says: "Our small office space in Wales was a challenge as most machines are manufactured to industrial cells, so Renishaw's experts advised us to go for the Ren AM 500Q. the machine's small size, speed and manufacturing accuracy made it a perfect solution."
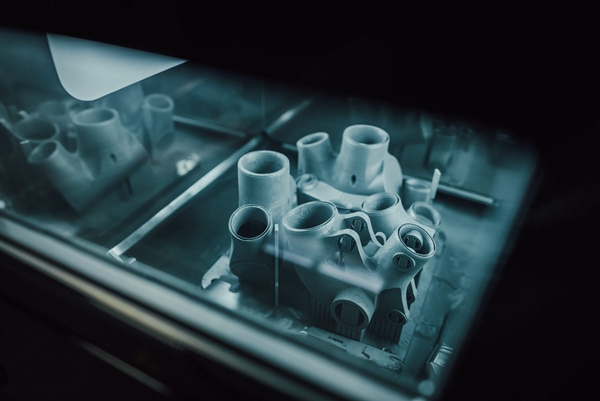
△ 3D printed titanium wheel set. Image from Atherton Bikes.
Renishaw's bicycle 3D printing expertise
Renishaw's additive manufacturing technology has been used by a number of bike manufacturers to produce their bikes and associated components for many years. Back in 2013, the company worked with Empire Cycles to create what is claimed to be the world's first 3D printed titanium bike frame, and since then companies such as Robot Bike Co and Bastion Cycles have used its machines to produce custom bike frames and other bespoke parts. Perhaps the company's most notable foray into the cycling industry was its work with Lotus Engineering and Hope Technologies to build a new track bike for the Great Britain cycling team. The bike was unveiled at the 2020 Tokyo Olympics and helped some of the team's cyclists reach the podium.
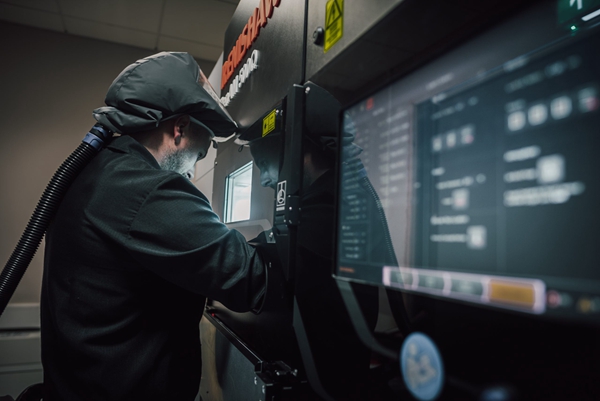
△Ren AM 500Q 3D printed bike parts for Atherton Bicycles. Photo from Atherton Bicycles.
3D printing of award-winning bike parts
Renishaw and Atherton Bikes first began working together in 2019 to produce 3D printed titanium lugs for the latter's bike frames. The lugs printed on the Ren Additive Manufacturing 500Q were designed to be both lightweight and strong to strengthen the connection between the tubes of the Atherton Bikes frame to better distribute the stresses the bike is subjected to in rough terrain. Bryan Austin, Sales Director of Renishaw's Additive Manufacturing Division, said: "By investing in an additive manufacturing process, Atherton has the design freedom to develop the best possible parts for its bikes, something that would be difficult to achieve using traditional casting methods. Casting using moulds is not suitable for producing the bespoke parts that Atherton's customers require. Casting only produces heavier parts and it does not produce the internal honeycomb structure that would be made lighter by 3D printing."
The two companies have now worked together to bring the lug's additive manufacturing capabilities in-house to better enable AthertonBikes' customers to test their new bikes in the Welsh mountains, just a short drive from their offices. brown says: "Renishaw has supported us throughout the process, from manufacturing the parts before we invested in the machine to installing and training our staff. Some of our colleagues were personally trained by Renishaw's engineer at New Mills, who makes our parts himself. His familiarity with our manufacturing processes enabled our staff to quickly adapt to the in-house manufacturing process after the training course."
Atherton Bikes invested in the Ren Additive Manufacturing 500Q, a compact quad-laser 3D printing system designed to dramatically increase productivity while improving the quality of the parts printed. With four 500W lasers, the system speeds up the manufacturing process by a factor of four, therefore expanding the range of applications that were previously uneconomical to produce via additive manufacturing. brown continues, "With this machine we are able to keep up with bespoke and high demand manufacturing requirements, especially during the busy race season. We are able to easily modify lug designs using computer aided design, allowing us to produce custom lugs quickly and re-produce them when necessary."
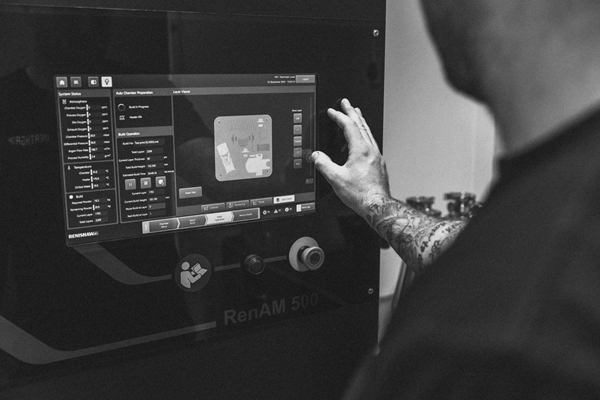
△Atherton Bikes can now produce 3D printed parts in-house at its factory in Wales. Image from Atherton Bikes.
Additive manufacturing allows pedals to be swapped for metal
Bicycle manufacturers are increasingly turning to additive manufacturing to optimise a range of components, as it can integrate multiple parts, reduce the weight of components and produce parts with previously unachievable geometries. Custom bike manufacturer Sturdy Cycles, for example, has chosen Headmade Materials' Cold Metal Fusion (CMF) technology to produce its titanium bike components and has previously worked with R Additive Manufacturing 3D to print parts for its road bikes. Elsewhere, bike component manufacturers Fizik and Specialized have used Carbon's DLS 3D printing technology to improve the weight and comfort of their bike saddles, while DQBD has used Stratasys' H350 additive manufacturing system to create fully personalised 3D printed saddles for improved performance efficiency.
3D printing's natural advantage for small batch manufacturing
There is no denying that for those small production runs, 3D printing has its own irreplaceable advantages in terms of economy and timeliness.
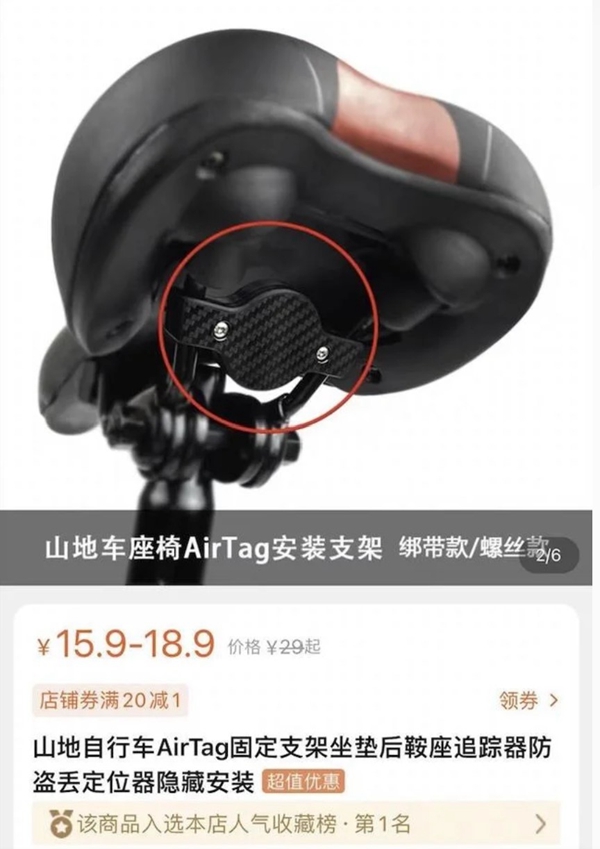
△Image source: Taobao
For example, Lei wanted to make a mount to hold his AirTag under his bike saddle. In the traditional way, Lei would have to make a wooden sample of the mount by hand, make a rough mould from silicone, make a fine sample from the rough mould, make a fine aluminium mould from the fine sample, and then make the final plastic mount from the fine mould. And if any of the steps needed to be adjusted in the middle of the process, Ray would have to start all over again.
Of course, Xiao Lei could have asked the factory for a mould to be made, but the cost behind this would have required hundreds or thousands to be produced at once, but Xiao Lei only had one bike, so it would not have been worthwhile. At this point the advantages of 3D printing came into play. Xiao Lei could skip the mould stage and make a model directly on the computer and then print it after slicing. Even if the result is not ideal, just adjust it on the computer and reprint it. It's true that buying a printer isn't cheap, but compared to the cost of days of time or the cost of opening a mould in a factory, the price of a second-hand print is "amiable".
This is why 3D printing technology promises to be one of the great turning points in manufacturing. The advent of modern 3D printers has lowered the barriers to manufacturing dramatically. Small companies can use 3D printing to rapidly iterate on product prototypes, the medical industry can rely on 3D printing to create customised implant solutions, and even the average user can use 3D printing to achieve "little crafts" that were previously unimaginable, such as printing a mouse case or true wireless headphones that fit 100% of their hand size. This is like a printer changing the way text is delivered.
Just as printers have changed the way words are delivered, consumer-facing 3D printers will revolutionise the way manufacturing is done in the future, with small, home-based workshops destined to be replaced by personal 'printing' devices, led by 3D printing. It will reshuffle the entire manufacturing industry.