3D printing,3D printed clothing,3D printing of cars,3D printed jewellery
12 July 2022 - The global luxury goods market is experiencing a rapid recovery from the pandemic and could reach €380 billion by 2025, according to a report published by the Italian Luxury Goods Manufacturers Foundation, Fondazione Altagamma and the strategic consultancy firm Bain & Company. In this growing market, the role of 3D printing in the luxury sector is becoming increasingly important. From accessories to eyewear, from high fashion to sports car parts, additive manufacturing has a lot to offer the demanding luxury market.
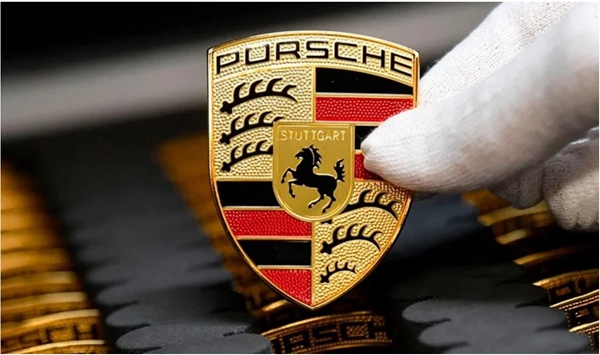
Companies such as Dior, Louis Vuitton, Bentley and Porsche have already taken the risk, convinced of the many benefits that 3D printing technology has to offer. However, many other well-known brands still refuse to use innovative options. Why are these companies still shying away from these opportunities? In any case, how can additive manufacturing be used in the luxury industry? To find out, this article discusses three fundamental pillars of the luxury industry: automotive, jewellery and haute couture, seeking to learn more about how luxury companies are implementing new technologies and the value they derive from them.
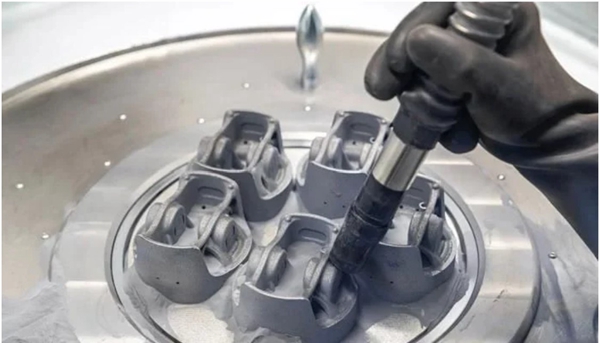
△ Pistons produced by Porsche using additive manufacturing (Photo credit: Porsche)
3D printing and luxury cars
Many luxury and sports car manufacturers tend to demand very high standards. Such car manufacturers need visually striking and extremely durable parts, and additive manufacturing is perfect for meeting these expectations. This technology makes it easy to manufacture complex shapes and enables lightweighting through the rationalisation of material applications. In addition, 3D printing offers a cost-effective way of producing small batches.
3D printing in the automotive sector
An important benefit of using 3D printing in the automotive sector is the ability to print more bespoke components from the factory, thus giving the car unique performance characteristics. British luxury car manufacturer Bentley is one of the companies that has successfully implemented it. Consumers spend thousands of dollars each year to customise their vehicles, and manufacturers can benefit from this by using additive manufacturing. another application of 3D printing is the creation of hard-to-find or obsolete parts. Increasingly, collectors and manufacturers of classic cars are working to restore and preserve certain models that are considered gems in the eyes of collectors. In addition to these two possibilities, another option for using additive manufacturing is becoming increasingly popular: 3D printing cars. Perhaps one of the best examples here is Divergent, a high-end sports car company based in California that produces ultra-lightweight car chassis and has an ambitious goal of designing all its car parts using 3D technology. But Divergent is not alone: 1016 Industries also provides 3D printing for luxury brands such as McLaren, offering optimised end parts.
"Our focus for this project was to explore how 3D printing could be used in the automotive sector, and the results of manufacturing these McLaren 720S parts are impressive. the 3D printing process has not only allowed us to manufacture faster and more efficiently, but also to improve quality. 3D printing technology has allowed 1016 Industries to make each part more accurately manufactured, with each part printed at a true scale to validate our CAD and CFD work." -- Peter Northrop, founder of 1016 Industries
In addition to this, 3D printing technology can provide fully functional prototypes for rigorous testing and simulation, tools for limited edition components, and ultimately small batch custom production parts for vehicles.
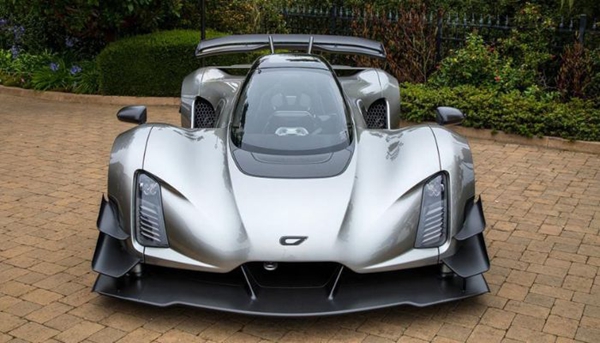
ΔDivergent3D's Czinger 21C luxury car (Photo credit: Divergent3D)
Most commonly used technologies
There are several 3D printing technologies used to produce automotive parts, depending on the final application, of course. For example, Porsche uses Powder Bed Fusion to create pistons from metal powder for the 911 GT2 RS. British luxury car designer Vital Auto uses SLA technology (also known as stereolithography) to produce other car parts such as air vents or door seals. Another of the most widely used technologies in this field is FDM, which is mainly used in the prototyping phase as it is a fast and efficient way of physically laying out components before final production.

The AstonMartin Callum Vanquish 25 will be equipped with several 3D printed parts (Photo credit: Makerbot)
Advantages of 3D printing in the automotive sector
3D printing reduces lead times: any part can be made in a matter of days or hours, even a scale model of the whole car, and at a much lower cost. In addition, 3D printing can handle thinner parts, more customised and bespoke designs, and different versions can be tested quickly and cheaply. One example is Bugatti, which 3D printed eight-piston monobloc brake calipers in titanium, saving money and improving performance by reducing the weight of the parts and making them more robust.
Additive manufacturing and high fashion
Many of the most high profile designers and companies in the fashion world have chosen 3D printing technology to create all kinds of clothes: dresses, bags, shoes, etc. If you look at some of the most important and luxurious events in the fashion industry, such as the Cannes Film Festival, the Met Gala or many of the world's major fashion shows, it is likely that someone is wearing a 3D printed dress.
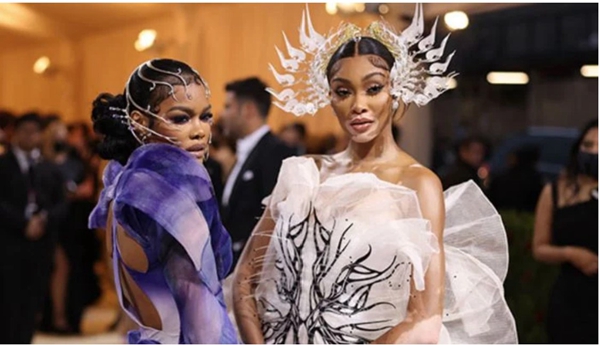
△TeyanaTaylor and Winnie Harlow in a couture dress by Dutch designer Iris Van Herpen (Photo credit: John Shearer)
3D printing in fashion
In the world of couture, 3D printing plays a very important role as it allows freedom of design that is not possible using traditional manufacturing methods. Thanks to 3D technology, it is possible to print different garments: one of these is shoes, such as the high-end shoe designer AnnieFoo. by scanning the customer's feet, the designer gets a piece that perfectly adapts to their shape, while providing a shape that is produced organically. As well as designers making customised garments for each client, there are also high-end companies that already have 3D printed shoes, such as Balenciaga, which retails for around $3,250.
There are also 3D printed garments, such as the designs by IrisVan Herpen, which transcend boundaries and fuse 4.0 technology with traditional craftsmanship.Iris' visionary designs blend groundbreaking technology and luxurious materials, often evoking a pre-war feel.
There are also high-end 3D printing companies that focus entirely on the fashion and luxury sectors, such as VOJD Studios, working with brands such as Kenzo, Acne Studios, Louis Vuitton, Alexander McQueen and Carolina Herrera to help them integrate 3D printing into their collections. Other companies, such as Dior, have used 3D printing to create thousands of prototypes and exact replicas of their collections to decorate their shops, such as the impressive 3D printed collection at the famous Dior Gallery in Paris.
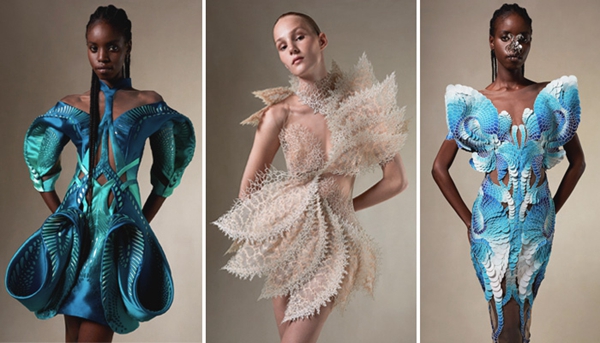
△Model from Iris van Herpen's Earthrise collection, in which 3D printing was used (photo credit: Iris van Herpen)
The most common 3D printing techniques used in the luxury industry
Currently, designers and creators are looking for materials that are quite soft and will evoke the look of leather or fabric. These vary depending on the garment to be printed. For rigid garments, different printing technologies can be used, such as SLA, LCD, DLP or SLS. this allows the fashion industry to create intricate designs with lots of detail, often for fashion shows. For more flexible garments, such as those designed by Israeli designer Danit Peleg, TPE is often used. TPE is an elastomer that can be stretched to the breaking point and has a high coefficient of friction, making it very pliable, so the result is very similar to a textile web. For these elastic parts, FDM is probably the most commonly used technology.
What are the advantages and disadvantages of additive manufacturing in luxury fashion?
In cutting edge industries like fashion, combining the latest trends with the latest 3D printing technology allows companies to stand out from their competitors. 3D printed designs are sustainable, more environmentally friendly and personalised. Bespoke has become a major trend in all luxury industries. Consumers of these products want unique garments, conceived just for them, which explains the success of brands that offer bespoke products. For Danit Peleg, who uses 3D printing in the production process, the main advantages of 3D printed fashion are individuality, flexibility and durability.
Danit Peleg explains: "There is zero production waste - there are no scraps or unwanted clothes in the shops. If you get bored of a garment, you can simply melt it down and make a new one."
One of the main drawbacks of 3D garments is their rigidity, which limits mobility. Currently, cotton and silk are more comfortable to wear and it would be interesting to find solutions to introduce more flexible materials or explore the concept of 3D printed knitwear in the future.
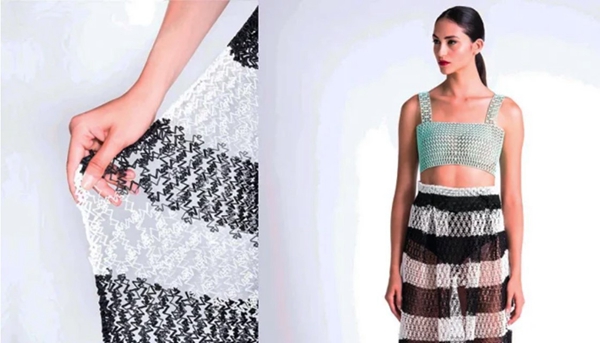
△ 3D printed clothes have a different texture to traditional products (Photo credit: Danit Peleg)
3D printing and jewellery
Jewellery making as an economic activity dates back 3,000 to 5,000 years to ancient Egypt. Century after century, jewellers have witnessed and played a leading role in successive technological innovations. But no technological advancement in the long history of jewellery has had as much impact as additive manufacturing. It has opened up a wide range of possibilities for jewellery designers, including customisation, aesthetics and speed of production. This is why world-renowned companies such as Cartier and Tiffany & Co. have integrated 3D printing into all stages of the production process, from prototyping to post-processing to the lost wax process.
How do we use 3D printing in jewellery?
3D printing is used in the jewellery industry in a number of ways, one of the most typical applications being prototyping. Additive manufacturing allows jewellers and customers to visualise parts before creating the final piece, albeit using different materials. This helps to improve designs, reduce the time needed for modifications and eliminate errors in the final design. On the other hand, we have the so-called indirect manufacturing methods. In these cases, 3D printing is used as a fast, accurate and efficient way to generate a basic model of the part. This model is then used to make a mould, which is produced and ultimately used to obtain the final part by casting and curing the final material of the part.
Another process used is lost wax casting, which allows for more complex shapes. This is a method in which molten metal is melted in place of the wax model placed in the mould. Jewellers can now 3D print this model, giving them more freedom in terms of geometry. Metal accessories for perfumes can then be produced, or aesthetic and technical accessories for leather goods.
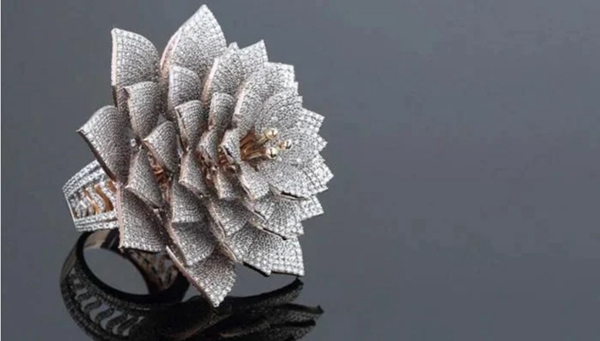
△ The ring that broke the world record for 7,801 diamonds! Design using 3D printed moulds (Photo credit: Imaginarium)
The most common techniques for making 3D jewellery
If there is one additive manufacturing technology that is very important to the jewellery industry, it is one that allows the manufacture of metal objects, such as laser fusion. Other companies, such as EAC, opt for metal binder jetting, which improves quality and productivity and guarantees a better finish for the parts. The most commonly used techniques are Stereolithography, valued for the level of detail it provides, FDM and Polyjet techniques. Stereolithography and FDM are common techniques for printing prototypes in hot melt materials and these techniques are mostly used in the traditional lost wax casting method for manufacturing jewellery parts.
Advantages and disadvantages of additive manufacturing in jewellery
With additive manufacturing, jewellers can be more efficient and productive, as they can focus on other tasks while the printer performs its function. In addition, thanks to additive manufacturing, it is possible to obtain several pieces with high quality and detail definition, especially in the case of complex and intricate designs. Despite the many advantages, not everything is rosy and buying a 3D printer requires an investment of time to learn how to model, as well as the money to purchase this new technology.
With 3D printing, there are no limits to creativity," says Patrick Chouvet, CEO of EAC. Additive manufacturing allows us to make and replicate any small part to continuously print and metalise parts. We are able to create, polish and metalise previously unimaginable complexity. With this new technology, we can meet any type of need. Additive manufacturing allows our designers and customers to design their accessories without any limitations."
The future of luxury 3D printing
As mentioned earlier, the luxury goods market is growing and represents high value. This makes it a key target market for 3D printed clothing, accessories, cars and more. Luxury customers, especially millennials, are increasingly looking to express their individuality through material goods such as clothing or cars. This is where the real appeal of 3D printed products lies: they offer great customisation and uniqueness, so designers using additive manufacturing processes, such as Iris van Herpen, have the opportunity to bring their products to an increasingly affluent market.
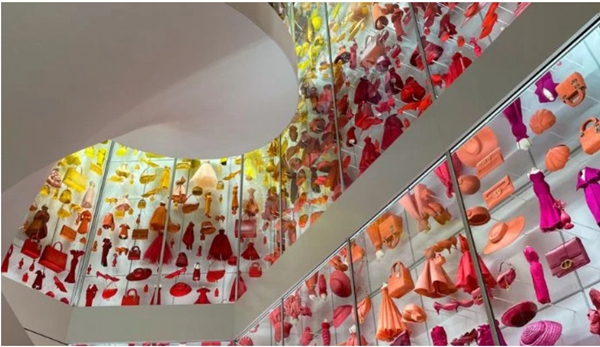
△ At the Dior gallery in Paris, thousands of pieces have been reproduced using 3D printing (Photo credit: Dior)
Furthermore, specific customers (such as the aforementioned millennials) or specific markets (such as the Chinese market) are always open to technological advances and sustainable clothing. As a result, their propensity to buy 3D printed luxury goods is likely to be positive. However, there is still a long way to go. In the fashion world, for example, 3D printing technology is not yet mature enough. We get unique designs, but they don't perform as well as traditional garments. Can we overcome this obstacle? I'm afraid that we still have to hope on new breakthroughs in additive manufacturing technology.